Customer Case - Kinnarps
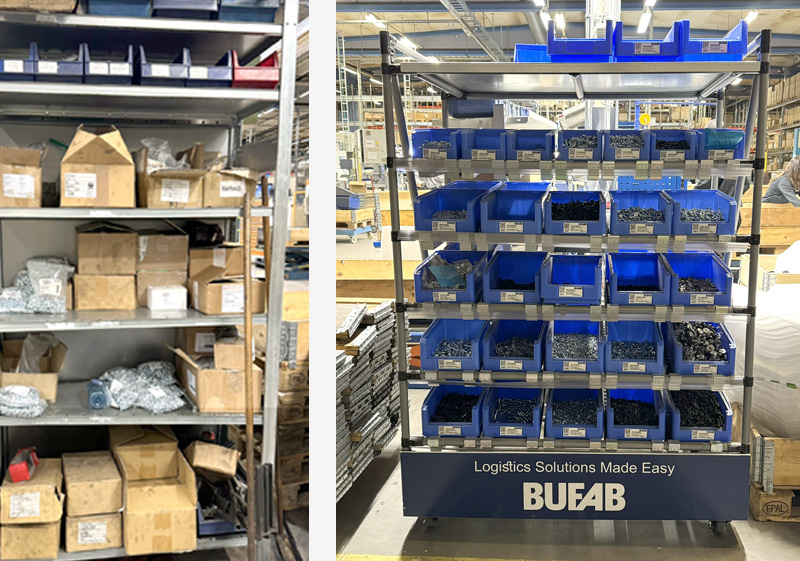
Kinnarps
Kinnarps creates interior design solutions and furniture for offices, schools and care environments, focusing on high quality, ergonomics and innovative design. The production facility in Jönköping mainly manufactures components for tables, chairs and screens for Kinnarp's own brands. Kinnarps is proud to bring back production from abroad into its modernised factory.
Anders Knutsson, Materials Procurement Officer, Kinnarps Jönköping
Jens Buchalle, Production Technician, Kinnarps Jönköping
About our cooperation
Bufab was already Kinnarps´s main supplier of fasteners and some other small technical items. Orders were made manually in Kinnaps´s ERP system.
Challenge
Placing manual orders was frustrating and time-consuming. That alone took about 30 minutes per day. The reception department received pallets of goods, which they registered, relabelled, and distributed to several points of consumption in production.
There was a mess on the material shelves in production, and it took a lot of time to put all the boxes in the right places. The staff did not always find what they were looking for and opened a lot of boxes. The mess created did not make it easy to place correct orders.
All in all, it was time-consuming, required heavy lifting, required individual knowledge and could still result in both stock shortages and overstocking.
Approach
A change was needed. Kinnarps and Bufab discussed and jointly decided that the flexible EasyScan solution with dual bins was the most suitable.
The operators just scan the empty bins, and an order is sent to Bufab. The same solution is applied to large-volume items in pallets.
The Bufab support worked exceptionally well during the implementation. Bufab made an initial labelling mistake but corrected it directly. Kinnarps had initial errors in inventory balances, resulting in shortages. Bufab made deliveries within hours.
Result
We will soon replenish all Bufab items through the EasyScan solution. We are sure that it saves us even more than we initially expected. Quick and easy and no hassle.