- Insights
- The Solutionists Hub
- Overcoming your inventory optimization problems — how to get started
Overcoming your inventory optimization problems — how to get started
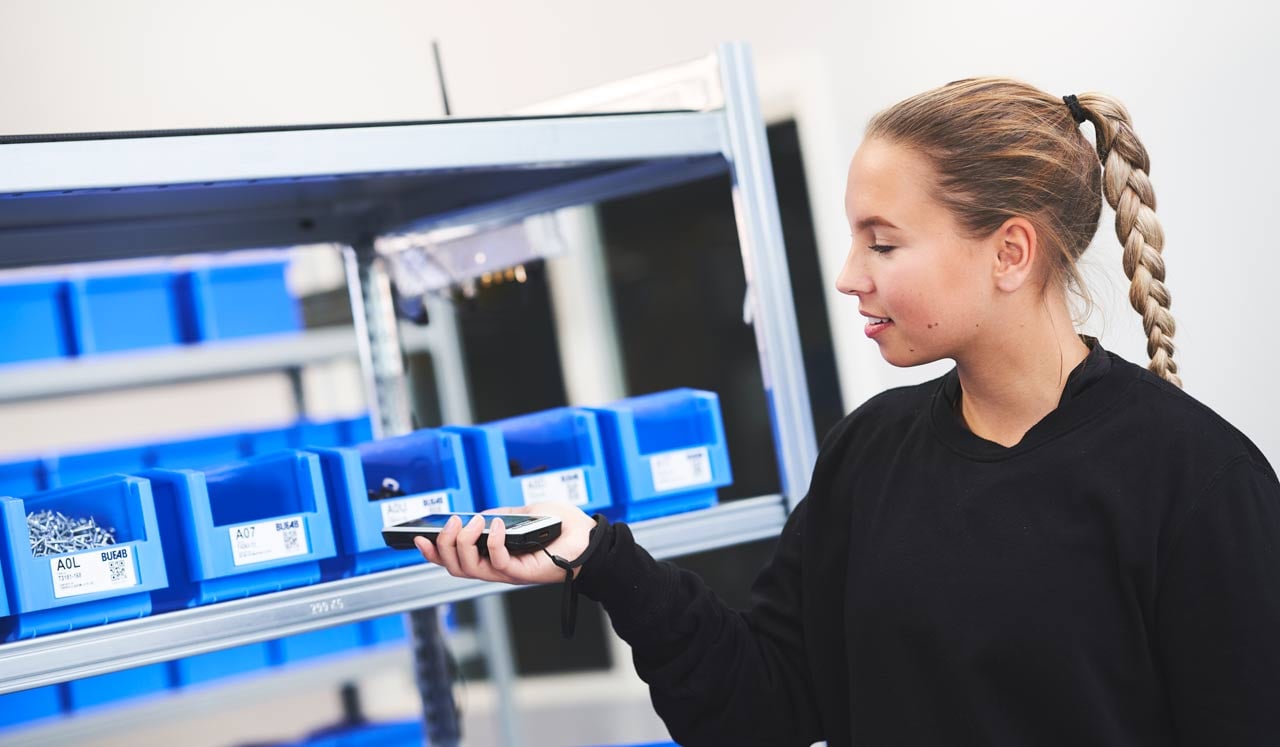
In my role at Bufab, I speak to many operations managers at companies that want to start improving their inventory management practices and companies that are already on the way.
Regardless of where they are in their journey towards a C-parts management process that works for them, they all have one thing in common – they know these small and seemingly insignificant components can create big problems if they're not handled properly.
The four problems that C-parts inventories can cause
In my view, poorly-managed and unoptimized C-parts inventories cause four common problems for manufacturing companies:
- They consume far too much time and energy – both on the production floor and in the back office
- They make it impossible to plan and make accurate forecasts
- They produce unreliable data on the actual number of C-parts currently in stock
- They cause inflexibility and make it hard to adapt to unforeseen circumstances
I've seen companies of all sizes and industries struggle with these problems, even companies with an otherwise highly optimized approach to production and logistics. To understand how these problems can be solved, let's look at why they arise in the first place.
What is an unoptimized C-parts inventory?
An optimized C-parts inventory is a system for storing your required C-parts that provides the components you need in the right quantity whenever you need them. An important quality of an optimized C-parts inventory is that it allows you to plan, forecast, and be confident that you will still have the fasteners you need if your requirements change. For example, suppose you know that you will ramp up production of a certain product in six months. In that case, your optimized C-parts inventory will allow you seamlessly increase the number of parts you have in stock in good time through smart, carefully planned replenishment. On the other hand, if you know that demand for a seasonal product will suddenly drop in a few months, you shouldn't have a large number of parts in stock that you won't use.
An unoptimized C-parts inventory, on the other hand:
- Leaves you with a shortage of parts at very short notice
- Can’t be quickly scaled up or down depending on your needs
- Isn’t easy to replenish with new parts when needed
As you can tell, the question of your C-parts inventory is partly the responsibility of purchasing, planning, R&D and logistics, as well as your colleagues in operations and production.
Why do so many companies have problems with their C-parts inventories?
I think the simple reason is that most people who deal with the C-parts, whether they're purchasers or operations managers, have so much to do with their A- and B-parts that C-parts come in third place. The journey an A- or B- part takes from being purchased to becoming a part of one of your products involves such a large amount of work from multiple departments that there isn't time left to spend on C-parts.
This is a necessary choice for many companies, but it causes problems – from poor or non-existent stock level information to production stops. And more often than not, these companies don't have the budget, time or competence to clear up their C-parts operation and create the same streamlined process they enjoy with their A- and B-parts.
Solving your C-parts inventory problems
To some degree, you can try to rectify these problems within your company – possibly by improving communication between production and purchasing, for example. However, in my experience, most companies struggle to achieve a lasting solution to the problem that doesn't consume too much of their time. When potentially hundreds of different components need to be organized and tracked in a central system, expertise is required that often doesn't exist in a typical manufacturing company – and even if it did, the time needed to implement this system would be impossible to find.
Consider parts consolidation, if applicable
It’s not always the case that the fewer types of parts you have to keep track of, the easier it is to manage your inventory. Of course, handling ten different items will always be easier than 100, but a well-optimized inventory will allow you to handle potentially thousands of different SKUs smoothly. However, you might hold higher volumes and more types of parts than you need – for example, if you were forced to make an excessively large order due to a high minimum order quantity, or if your product offering has grown and now requires many different types of very similar components.
While simply slimming down your inventory won’t necessarily make it optimized, it can at least make life easier – working with some kind of supply chain partner can help you overcome the biggest issues that high MOQs can cause, but it’s also the job of your design and R&D departments to remove the unnecessary components from the products you manufacture. It’s difficult to consolidate the number of parts used in products that are already in production, so over time, it’s vital to minimize the number of new parts that are introduced via new products. Ideally, the design department should look at the components that are already in use in existing products and start with them when designing new products.
Focus on reducing your number of suppliers
My colleagues have written extensively about supplier consolidation on The Solutionists Hub before, so I won't go into too much detail here. However, for many of the companies I meet, an unoptimized C-parts inventory is made worse by a huge number of C-parts suppliers, each supplying a small number of parts. Keeping track of hundreds of different ordering processes and deliveries from each supplier makes the inventory hard to handle – so if you rely on many suppliers for your C-parts, consolidating your orders to one or a few bigger suppliers will instantly solve a lot of issues.
Look into your available logistics solutions
Most companies with C-parts inventory issues would benefit from a logistics solution. Setting up logistics solution systems requires an analysis of your historical parts needs and your schedule for the future – but once they're in place, they remove inter-department communication issues and the inflexibility of the traditional manual ordering process.
Whether the solution is based on production staff manually scanning a bar code on a bin or a scale that constantly tracks the number of remaining parts by measuring the bin's weight, it allows new parts to be ordered automatically in good time and avoids time-consuming manual orders and parts shortages.
C-parts might not be at the top of your mind when you’re managing your daily production work – but if they're ignored, they can quickly create serious practical problems and cost a lot of money. Giving C-parts the attention they deserve and building a structure that ensures you don't have to spend so much time managing them cures many headaches.
If you want to find out more about your options, download our logistics solutions guide to get an explanation of the most common alternatives and their benefits and disadvantages. You can also read our guide to C-parts optimization to get some wider information about how to keep your parts store running as effectively as possible.