- Insights
- The Solutionists Hub
- Sustainability targets and KPIs to implement in the purchasing department
Sustainability targets and KPIs to implement in the purchasing department
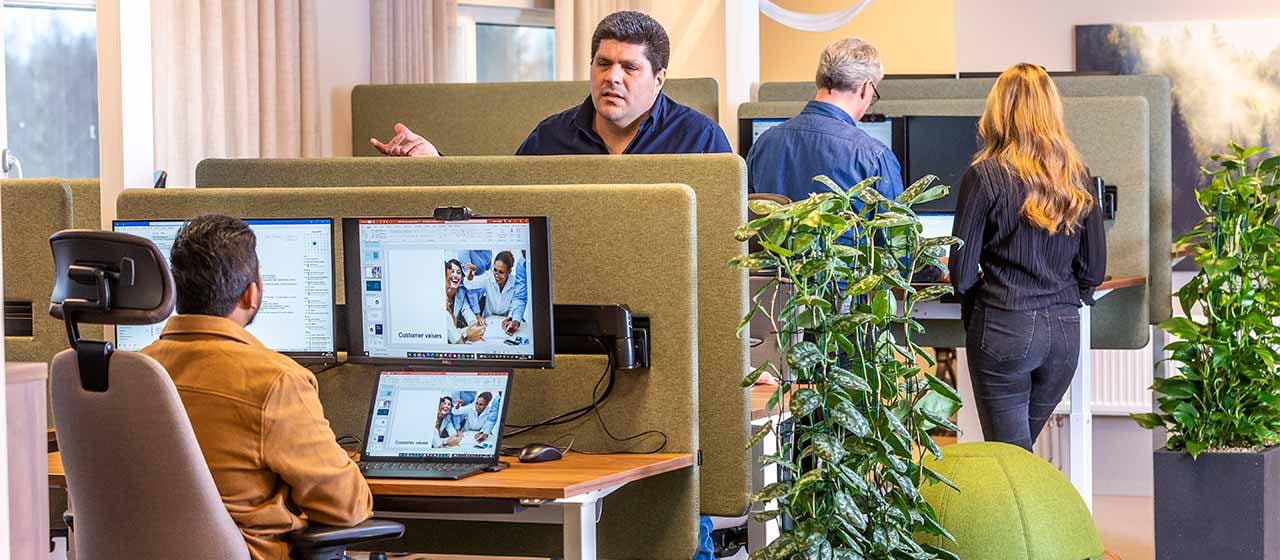
As sustainability has become more and more of a priority for manufacturers, the approach these companies take to the topic has matured. In 2023, it is no longer enough for a company to simply talk about its commitment to sustainability – they also need to show proof. To do this, new metrics need to be recorded and analyzed, and new targets and KPIs need to be put in place to guide the company’s priorities and create a common goal.
If you deal with C-parts in a purchasing or sourcing role at any manufacturing company, you probably follow a few core Key Performance Indicators (KPIs) and targets. For example, you might have a target to consolidate your number of suppliers. Other targets may be related to costs and your total spending. You might also have KPIs linked to lead times or unplanned emergency orders, which help the production line keep rolling smoothly.
Without measuring metrics like these, you cannot set KPIs, and without KPIs, you cannot decide which areas of the purchasing operation need attention. Whatever your specific KPIs are, they are essential for tracking progress and improving your performance over time. So, when new regulations and different stakeholders such as customers and shareholders are pressuring your company to boost sustainability, new KPIs are essential for making real progress.
The sustainability-related targets and KPIs implemented in your company will differ depending on how your supply chains work and which market you operate in. But to give an idea of the kinds of pressures that purchasers may be facing soon, here are some sustainable KPIs that I have come across in my work:
Sustainability audits on suppliers
Auditing suppliers on their level of sustainability through physical visits can be costly and time-consuming – but it’s also the best way to get to the facts about the supplier’s level of sustainability and uncover any problems that need to be resolved, for example, in health and safety practices at the supplier’s factory.
Once an independent supplier audit is completed, you can feel more confident that this supplier can live up to the demands laid out in your sustainability policy. However, auditing all suppliers at once is not feasible for many manufacturers. Instead, it can be broken up into phases or turned into a time-bound KPI — for example, you could decide to prioritize partner suppliers and say that by 2028, all partner suppliers representing 70% of your total purchasing spend, for example, will have gone through a sustainability audit. Since they stand for most of your C-parts supply, you can make the most significant impact on the overall sustainability of your supply chain by focusing on them first.
Sustainability policies or certificates in place
Even if your company has a well-designed and exhaustive sustainability policy, there are increasing demands to make sure your suppliers are committed to the same approach. For that reason, one relevant KPI could be the percentage of suppliers who have developed their own sustainability policy or their success in meeting their own sustainability KPIs.
Similarly, you could also look at the types of independent sustainability certifications the supplier may or may not have. Organizations like EcoVadis, for example, conduct sustainability assessments and provide ratings to companies based on their sustainable performance. Working to gain ratings like these demonstrates a commitment to sustainability within an organization, so the proportion of supplier companies with sustainability certifications in place may be a relevant KPI.
Rate of obsolescence
This KPI could easily be expressed as a percentage that you can track and compare over time – what percentage of all the parts in your inventory is currently obsolete, or what percentage has become obsolete over the last 12 months? There can be many reasons that parts become obsolete, from discontinued products to changed designs. However, letting obsolescence get too high is not only a waste of money – it is also a waste of the energy, fuel and materials required to produce and ship the parts to you. If your company wants to become sustainable, efficient and effective handling of inventory is essential, and to keep waste to an absolute minimum, you cannot afford to let your rate of parts obsolescence rise.
Carbon emission targets
With all the focus placed on the environmental aspects of sustainability, emissions have become a core focal point for many manufacturers. Chances are, this is already a KPI in place across your company. But when thinking about emissions, it is important to consider emissions scopes.
Scope 1 emissions come from sources your company directly owns or controls – for example, diesel-powered forklifts that operate in your warehouse.
Scope 2 emissions are not as directly related to your company, but they are still relatively simple to reduce. These are the emissions created by the generation of the energy you buy – for example, the electricity at your office. Switching to more energy-efficiency machines or increasing your use of renewably generated electricity could help reduce these emissions.
Scope 3 emissions are all the other emissions that you are responsible for but do not directly control or produce yourself. All the emissions generated in your supply chain – during the manufacturing and shipping of your C-parts, for example – fall into the scope 3 category.
When thinking about your emissions, it is important to distinguish between these three. Scope 1 emissions can be relatively simple to bring down — for example, by replacing company cars with electric vehicles. Scope 2 emissions can be reduced by purchasing electricity from renewable sources. Scope 3 emissions, on the other hand, are naturally more difficult to reduce because you do not have full control over them. In order to bring them down and meet your company’s emissions targets, you will need to collaborate with suppliers or supply chain partners to optimize multiple stages of the product journey.
Consumption of energy and water
When thinking about environmental sustainability, carbon emissions caused directly by manufacturing and shipping processes have historically received the most attention. However, questions about water use and consumption of energy (both from renewable and non-renewable sources) for other purposes than for direct manufacturing are just as important.
With energy shortages becoming a real risk for businesses and water shortages impacting more and more people around the world, optimizing their use as much as possible is critical for sustainability. Water use can be measured simply in liters, and you can start by looking at ways to reduce water usage at your own production facility.
The same applies to electric power – even if it is generated by solar or wind, minimizing consumption is essential, since electrification will see demand for electricity grow dramatically in the coming decades.
Social sustainability KPIs and purchasing
The social aspect of sustainability is a vital component, along with environmental and economic sustainability. However, many companies find it difficult to set relevant KPIs in this area. Emissions and energy use are easy to quantify by looking at the tons of released carbon or kilowatt hours used in your operations. Questions about working conditions, wages, and fair treatment are not as easy to express in numbers. However, international standards organizations such as the Global Reporting Initiative have some KPIs that reflect these hard-to-define qualities in simple figures. For example:
- Types and rates of workplace injury
- General rates of absenteeism
- Average hours of training per year, per employee
- Number of grievances about labor practices addressed through formal channels
The list can be made much longer – but by consulting the established standards, it is possible to turn vague measurements into KPIs that can help you optimize your supply chain to become as socially sustainable as possible.
To keep learning more, make sure to read more of our insights on the role of C-parts in sustainable supply chains, or download The Manufacturer's Guide to Sustainability Trends below to see the developments in sustainability that will affect your C-parts operation in the coming years.
Get new knowledge every week!
Related
-
By Kadi MeriväljaC-Parts Purchasing: Handling Your Sustainable Purchasing Policy
-
By Patrik Lundström TörnquistSustainability Challenges With C-Parts, and How to Manage Them
-
By Carina LööfSustainable C-Parts: What You Need to Know
-
By Niklas LindsköldCBAM: How will it affect European manufacturers?
-
By Niklas LindsköldHuman rights due diligence: Is your supply chain under control?
-
By Niklas LindsköldChemical compliance: What manufacturing companies need to know
-
By Niklas LindsköldConflict minerals: How to avoid them in your manufacturing operation