- Insights
- The Solutionists Hub
- Sustainability Challenges With C-Parts, and How to Manage Them
Sustainability Challenges With C-Parts, and How to Manage Them
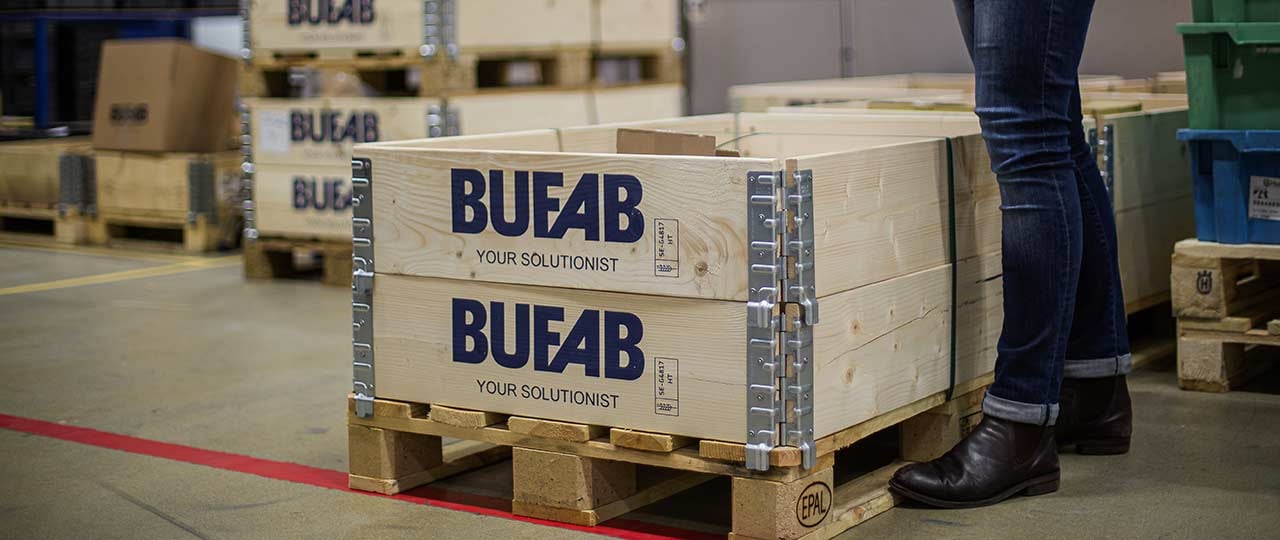
If you're part of a manufacturing company, you'll know that sustainability is an essential part of your operation. Today, companies like yours are facing more pressure than ever from customers, stakeholders and shareholders to boost the company's sustainability in a concrete and measurable way.
This pressure is likely felt across your company – from purchasing and planning to production and R&D. In response to changed behavior and environmental regulations, many manufacturers have become quite good at documenting and improving their internal sustainability practices and proving the sustainable origins of the A- and B-parts they use – however, from what I've seen, few give the same level of attention to their C-parts.
It's great that sustainability across the supply chain is getting the attention it deserves, but it's a shame that C-parts don't have the same priority as other components. That's because this class of components creates some unique sustainability challenges that manufacturers will have to deal with if they want to reach true sustainability across their entire product range.
In this article, I'll explain the concrete challenges that C-parts can pose in your work:
Reporting emissions as a manufacturer
Calculating and reporting the carbon emissions generated by the manufacturing process is becoming more or less necessary for many firms. After all, if you haven't measured your emissions, you can't work to reduce or offset them. It's a vital first step towards becoming a more sustainable company, but doing it properly requires time, hard work, and a great deal of knowledge about your suppliers and your C-parts supply chain.
Lots of businesses have a good picture of their scope 1 emissions. These are emissions that the company produces directly – emissions released during your manufacturing process or from sales reps' cars during customer visits are good examples of scope 1 emissions. These can be a real challenge to calculate, but it's possible to do it yourself with the right internal reporting practices in place. Reporting on scope 2 emissions, indirect emissions created by the electricity you purchase, is also feasible for most companies. However, scope 3 emissions are usually the ones that cause the problems. These are all the other emissions released in the company's entire value chain, from start to finish. So, to accurately calculate the emissions generated by your company's use of a particular type of steel bolt manufactured in Asia, you would need to consider the emissions generated by:
- The extraction and refinement of the raw materials
- The production of steel from these raw materials at a steelworks
- The manufacture of the bolts
- The international shipment of the bolts
- Delivery from the port to a central warehouse
- Delivery from the central warehouse to you
- The use of your product after purchase
- Potential product returns and possible disposal at end-of-life
- The waste that is created and the emissions generated by the transport of goods at all stages of the process
Even if you have lots of time on your hands and an expansive knowledge of your supply chain, you'd probably struggle to calculate these emissions for yourself.
How to make emissions reporting easier
For an accurate measurement of scope 3 carbon emissions, most manufacturers should probably turn to an external partner. Regardless of your industry, there's a large number of businesses that are experts at measuring the emissions generated in your supply chain.
This option works well if you're happy to stick with your existing C-parts purchasing process. However, if you're open to making a more impactful change, it would be smart to choose a supply chain partner like Bufab who can handle your C-parts sourcing, purchasing and shipping while also reporting on the emissions this work generates.
Improving supplier sustainability
You may have invested in renewable power sources, more efficient equipment and excellent waste management systems at your production site, but if your C-parts come from unsustainable sources, your actual effect on the environment may not be as positive as you think.
Unfortunately, verifying the sustainability of your supplier base and working with them to make improvements is simply out of scope for many manufacturing companies – especially those based in Europe with a supplier base primarily located in the Far East. Companies like these face a language barrier and high travel costs when they visit their suppliers. And if they deal with suppliers directly rather than through a partner, they probably don't have too much influence. For the supplier, they're likely just one customer out of many, and even if they have a good relationship, the supplier is probably not willing to make big changes in their business, manufacturing and logistics practices for their sake.
I've mentioned the Far East as an example here, but the same can apply to suppliers in other regions. Unfortunately, many inaccurate stereotypes about manufacturing in Asia may be actively harming your company's sustainability efforts. In many respects, some manufacturers in Asia are well ahead of European competitors regarding renewables and sustainability. From a sustainability point of view, it may be better to source parts from a modern, sustainable supplier in China and have them shipped by sea than having parts freighted by road from a European supplier that uses dirty fossil energy to power their factory.
The challenge of distinguishing between these two extremes can be huge if you lack the proper knowledge about sustainability or feel you don't have enough influence over the supplier. Again, in my opinion, the only way to guide your suppliers in the right direction and improve your sustainability through them is to work with a partner like Bufab – ideally, the larger they are, the better. Put simply, you will struggle to make an impact as a single company – but as one of many companies that sources and purchases through a much larger partner, you gain a lot more influence and a larger pool of alternatives if your preferred supplier still isn't responsive.
Parts management mistakes that can lead to unsustainable practices
The very nature of C-parts themselves, and the way that lots of companies approach them, can quickly damage any sustainability initiatives. If your company has issues with its C-part supply, you've probably experienced unexpected parts shortages, long lead times, and high minimum order quantities. C-parts are often cheap and generic parts, so, understandably, companies don't focus on them as much as their A- and B-parts. However, when they're ignored, structural issues like unoptimized parts inventories and unconsolidated supplier bases can grow over time.
From a sustainability perspective, this can be disastrous – poor C-parts management leads to sudden shortages, which can force you into making highly inefficient express orders of small quantities of parts, sometimes shipped by air. A mistake like this can quickly erase months of improving sustainability and reducing emissions elsewhere in the company. Similar issues can occur if high MOQs leave you with a large stock of obsolete components when you stop producing a particular product. Even if metal is highly recyclable, disposing of these parts wastes the energy needed to produce and ship them. And while a large, unconsolidated supplier base can cause a long list of issues, the worst in sustainability terms is the need for multiple shipments of small quantities of parts rather than one larger one from a single supplier.
You need to tackle these issues to improve your company's sustainability on a foundational level. But they're more complex than simply installing solar panels on the office roof – they require a change in your entire approach to C-parts. Achieving this change is our core business, but there are steps you can take yourself – for example, by trying to source more of the parts you need from fewer suppliers or improving internal communications to avoid planning mistakes that lead to express deliveries.
Some of my colleagues have covered the major issues that C-parts, a seemingly insignificant part of your business, can cause to your manufacturing operation. I hope I've shown that they can cause just as much damage to your sustainability initiatives. When manufacturers are facing such pressure to make their businesses more sustainable, make sure you don't neglect C-parts.
Download the guide to sustainability trends
If you're looking for some further reading, click below to get the guide to sustainability trends for manufacturers. It covers the most relevant factors within sustainability that your company will soon start dealing with, from regulation to reshoring, and focuses particularly on your C-parts supply chain. Take a look if you want to get prepared.
Get new knowledge every week!
Related
-
By Sergio BrambilaSustainability targets and KPIs to implement in the purchasing department
-
By Kadi MeriväljaC-Parts Purchasing: Handling Your Sustainable Purchasing Policy
-
By Carina LööfSustainable C-Parts: What You Need to Know
-
By Niklas LindsköldCBAM: How will it affect European manufacturers?
-
By Niklas LindsköldHuman rights due diligence: Is your supply chain under control?
-
By Niklas LindsköldChemical compliance: What manufacturing companies need to know
-
By Niklas LindsköldConflict minerals: How to avoid them in your manufacturing operation